I don't quite get it. How come the air used for cooling is not available to drive the turbine?. Isn't it supposed to pass through the fuel-air heat exchanger then still go into the turbine, just slightly hotter?.39 years as a Customer Support / Field Service Engineer for P&WDo you have additional source for that or it come from your experience working on these engine?.Yes, the F135 is supplying 30kW of bleed flow for 3F. However, this requires the engine to run hotter and faster to offset this diversion of core airflow, which reduces hot section life, driving the power module back to depot sooner than planned.
Anyway, I find this pretty interesting since F-18E/F intended to provide 15kW liquid cooling for APG-79. Given that APG-81 has a bit more T/R modules than APG-79 (1626 modules vs 1368 modules), I wonder what the cooling requirement for APG-81 would be. Maybe 19-20kW?
View attachment 677766
Taking bleed air from the core airflow is a double penalty for engine performance. All of the air taken from the compressor has absorbed turbine power to get it pressurized - this lost turbine power has to be offset by pushing more fuel and temperature into the combustor. And this air is no longer available to drive the turbine, which means further fuel and temp increase. And the impact is increased at altitude where air density is lower but the cooling demands remain relatively constant.
This increased bleed flow pushes up the operating temperatures throughout the flight envelope. The engine performance is reduced when against the max operating limits, and the temperatures are increased at all other operating conditions, cumulatively using up available hot section life.
Also if I understand correctly, this method of using engine air seem to generate much higher cooling capacity compared to the traditional ambient air scope right?. The air flow is obviously higher because the engine such air in?.
I recalled the cooling capacity of the big F-15E is only around 35kW, so for the medium size F-35 to have 30 kW cooling from its engine alone seem quite impressive. Then it probably get another 5-10 kW of cooling through the top left side cooling scope for a total of 40kW cooling
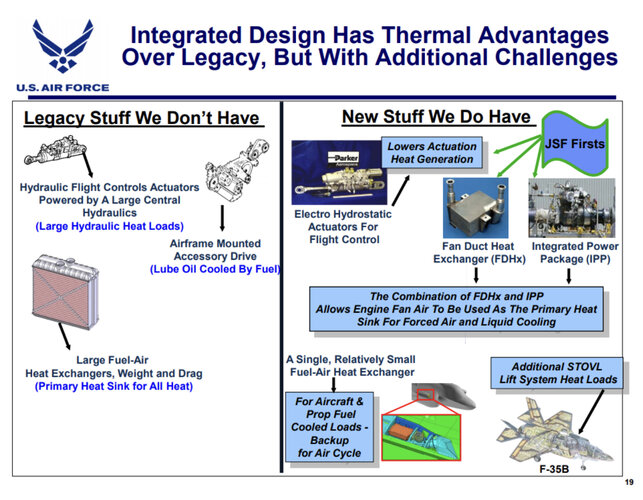
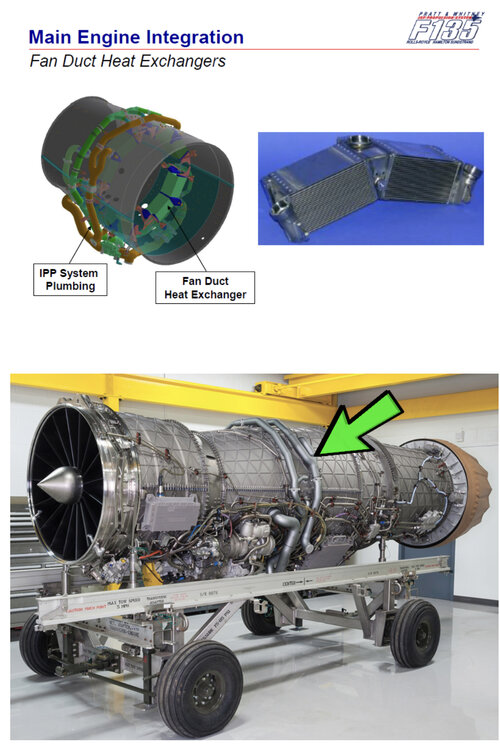