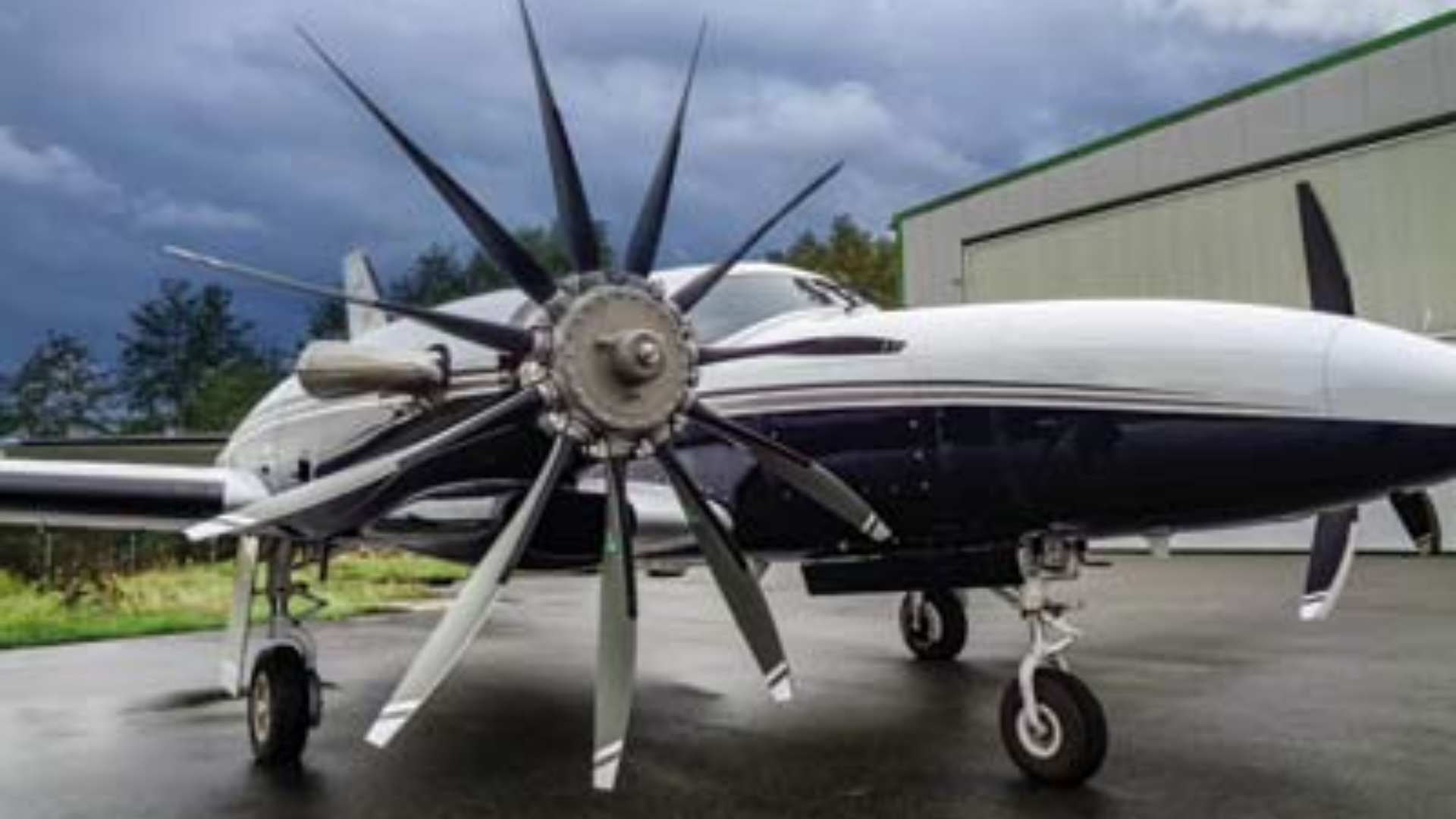
World's first propeller with 11 blades completes first test flight
MT-Propeller has successfully demonstrated propellers with seven and nine blade prior to this with promising results.
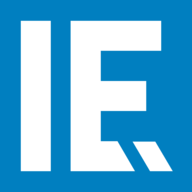

Like wing aspect ratio I figure longer thinner blades would technically be more efficient at producing “lift” but there may be speed efficiency curve issues that may limit altitude performance and max speed? Turbofan blades have moved to being wider and fewer, and even being mildly supersonic at take-off thrust but the duct and lack of pitch control creates a different working dynamic and set of requirements.Are 11 thin blades better than 5 or 6 wider ones?
Generally noAre 11 thin blades better than 5 or 6 wider ones?
There's a bunch of tradeoffs (I did prop aero for several years), but generally if you spread needed blade area over more blades efficiency increases as induced losses are less. However, structural considerations will put a minimum limit on individual blade chord, hence area. Crowding between blade roots may cause shocks at high speed, reducing prop efficiency.Generally noAre 11 thin blades better than 5 or 6 wider ones?
Fewer high aspect ratio blades on as large a propellor diameter as possible should be most efficient.
But if you are limited by diameter and need to put more power through the disk then you need to increase blade area, from either more blades or wider chord blades
I wonder if noise and vibration is the real driver here. More blades shifts the tones so it might not seem as loud.
There are basic diagrams charting engine config type with efficiency at general speed ranges. Those whirligigs remain a popular way to move aircraft and I really would love to see a prop fan make it to service. Case in which the need for turbofan-like cruise performance required swept, wide chord blades made from carbon fiber for strength at such large size and design. Those technologies did made the GE90 and many newer turbofans possible - themselves having propfan approaching efficiency.I would be negatively (which in my own personal worldview of being a pessimist means not really) surprised if someone had not yet developed an algorithm to determine the answer to that very exact question. It would be nice to see a big multidimensional matrix of airspeed/fuel consumption/propeller design/engine type/fuel, but then again, I'm firmly a jet/rocket guy myself - why waste any effort on open air exposed whirligigs that really have to struggle to even get to Mach 1?
Theodorsen pretty much solved propellers. Unfortunately it came right on the tail end of piston engine aircraft. I'd guess that the few companies who really need high performance props with big turboprops have done what you've asked, but they aren't sharing their methods.I would be negatively (which in my own personal worldview of being a pessimist means not really) surprised if someone had not yet developed an algorithm to determine the answer to that very exact question. It would be nice to see a big multidimensional matrix of airspeed/fuel consumption/propeller design/engine type/fuel, but then again, I'm firmly a jet/rocket guy myself - why waste any effort on open air exposed whirligigs that really have to struggle to even get to Mach 1?
A good chunk of a propeller's blades are stalled during takeoff. This prop may have more unstalled regions than their baseline or it has too much area for optimal cruise performanceMT is a company which knows what they are doing. The video sound might not be 100 % accurate, but the plane is totally missing the familliar propeller sound. It is very reasonable to believe, that they really archieved a very great noise reduction.
MT also mentioned 15 % higher trust at zero speed, this is nice to have, but the efficiency at cruise speed would be of intrest...
There's alot of complexity in having that many pitchable blades in such a small package but we have many newer technologies to produce more complexity for a given cost. This could be a real game changer for STOL planes really needing that 15% extra thrust as Nicknick mentioned in post #14, but such civil platforms are cost constrained from the get-go by operators. Producing 9 and 11 blade props needs to be affordable for the market that needs it most. Otherwise this really could just be a PR exercise or a showcase for potential military ops.Theodorsen pretty much solved propellers. Unfortunately it came right on the tail end of piston engine aircraft. I'd guess that the few companies who really need high performance props with big turboprops have done what you've asked, but they aren't sharing their methods.I would be negatively (which in my own personal worldview of being a pessimist means not really) surprised if someone had not yet developed an algorithm to determine the answer to that very exact question. It would be nice to see a big multidimensional matrix of airspeed/fuel consumption/propeller design/engine type/fuel, but then again, I'm firmly a jet/rocket guy myself - why waste any effort on open air exposed whirligigs that really have to struggle to even get to Mach 1?
This looks more like a PR stunt than anything else to me. Its hard to see how 11 blades would be worth it, even if the prop diameter is really constrained.
“Thus Returns Hartmann The Anarchist:”I am tempted to add both the 'steampunk' and 'cyberpunk' tags to this thread.![]()
I'd say most likely yes, given this from the attached article,I wonder if noise and vibration is the real driver here.
MT-Propellers' five-bladed propellers have lower noise and vibration levels and have quickly become the industry standard. They are used on a wide range of aircraft, such as the Cessna 425 Series, Piper Cheyenne PA31T and T1, Piper Cheyenne PA42-1000, and Cessna 208 Caravan aircraft.
This is all about noise reduction, though a 15% boost in takeoff thrust is a very nice bonus.This looks more like a PR stunt than anything else to me. Its hard to see how 11 blades would be worth it, even if the prop diameter is really constrained.