Interesting emission- and contrail reduction concept - a long description and a shorter one:
www.mdpi.com
aeroreport.de
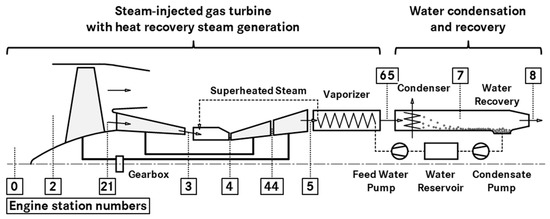
The Water-Enhanced Turbofan as Enabler for Climate-Neutral Aviation
A significant part of the current aviation climate impact is caused by non-carbon-dioxide emissions, mainly nitrogen oxides (NOx) and contrails. It is, therefore, important to have a holistic view on climate metrics. Today’s conventional, but already well-developed, aero-engines are based on the...
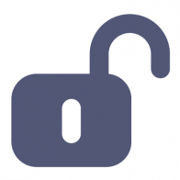

A brief guide: How the WET concept works
The water-enhanced turbofan is a gas-turbine-based concept that approaches climate neutrality.
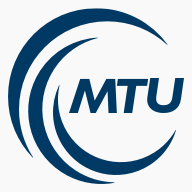